Kits¶
In Odoo, a kit is a type of bill of materials (BoM) that can be manufactured and sold. Kits are sets of unassembled components sold to customers. They may be sold as standalone products, and are also useful tools for managing more complex bills of materials (BoMs).
Note
To use, manufacture, and sell kits, both the Manufacturing and Inventory apps need to be installed.
Create the kit as a product¶
To use a kit as a sellable product, or as a component organization tool, the kit should first be created as a product.
To create a kit product, go to New.
, and then clickThen, assign a name to the new kit product. Next, set the kit’s product type depending on inventory tracking needs and accounting requirements. To do this, under the General Information tab, set the Product Type to Goods and either check the box next Track Inventory if inventory tracking is required, or leave it unchecked if inventory tracking for the kit is not necessary.
See also
Learn more about tracked versus untracked products.
The kit’s components must also be configured as products via
. These components require no specific configuration.Untracked kit inventory setup details¶
Consider leaving tracking for the kit’s inventory untracked when the kit is used in other manufacturing processes or when tracking inventory for the kit itself is not needed.
Recommended for Continental Accounting: If costs are expensed immediately upon purchase, then leaving the kit’s inventory as untracked is recommended.
Replenishment via Components: Inventory count is managed at the component level, so reordering rules must be set to individual components.
Selling & Stock Constraints: Kits cannot be sold if any required component is out of stock. Since availability depends on individual components, a sales order may appear valid, but delivery can be delayed if components are unavailable.
Tracked kit inventory setup details¶
Consider turning on tracking for the kit’s inventory when the kit is a tangible product or warehouse and inventory tracking is essential.
Recommended for Angle-Saxon Accounting: If the Cost of Goods Sold (COGS) needs to be recorded in journals, then tracking the kit’s inventory is recommended.
Component Purchase Constraints: Only the kit’s minimum required components can be added to an eCommerce cart unless the option to continue selling is disabled.
No Kit Serial Numbers: Serial number tracking does not track the kit, only its shipped components.
Reordering Rule Recommendation: Reordering rules should be set at the component-level.
Stock Replenishment Recommendation: Stock replenishment should also be done at the component-level.
Kit setup similarities¶
Regardless of which setup is used, there are some similarities between the two options.
No Kit-Level Stock Adjustments: Stock adjustments cannot be handled at the kit-level.
Kit Value Does Not Change: The stock’s value is the same whether the kit’s is tracked.
Kit Internal Transfers: An internal transfer for the kit breaks it into components.
Set up the kit BoM¶
After fully configuring the kit product and its components, a new BoM can be created for the kit product.
To do so, go to New. Next to the Product field, click the drop-down menu to reveal a list of products, and then select the previously configured kit product.
, and then clickThen, for the BoM Type field, click the Kit option. Finally, under the Components tab, click Add a line, and add each desired component, and specify their quantities under the Quantity column.
Once ready, click Save to save the newly created BoM.
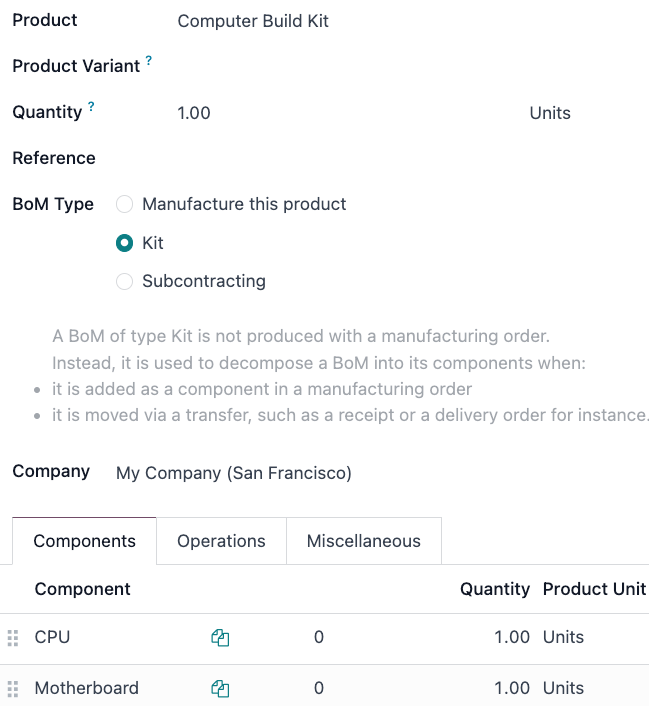
If the kit is solely being used as a sellable product, then only components need to be added under the Components tab, and configuring manufacturing operations is not necessary.
Note
When a kit is sold as a product, it appears as a single line item on the quotation and sales order. However, on delivery orders, each component of the kit is listed.
Use kits to manage complex BoMs¶
Kits can also be used for complex BoMs. This method nests BoMs within other BoMs, organizing complex products while simplifying manufacturing by defining each procurement and production step separately.
Sublevel BoMs (subassemblies or semi-finished products) streamline these workflows, helping with traceability efforts.
See also